Hoisting technology and scheme of steel structure
- Share
- Issue Time
- Jan 4,2021
Summary
Steel structure building positioning --- steel structure elevation --- steel structure column top bolt embedding --- elevation --- snapping line --- steel structure column installation --- steel beam installation --- secondary structure installation --- welding --- touch up painting --- completion
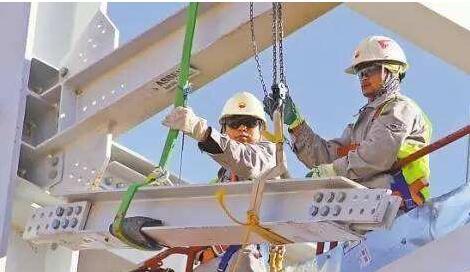
Hoisting technology and scheme of steel structure buildings(warehouse, workshop,office,hospital,dormitory)
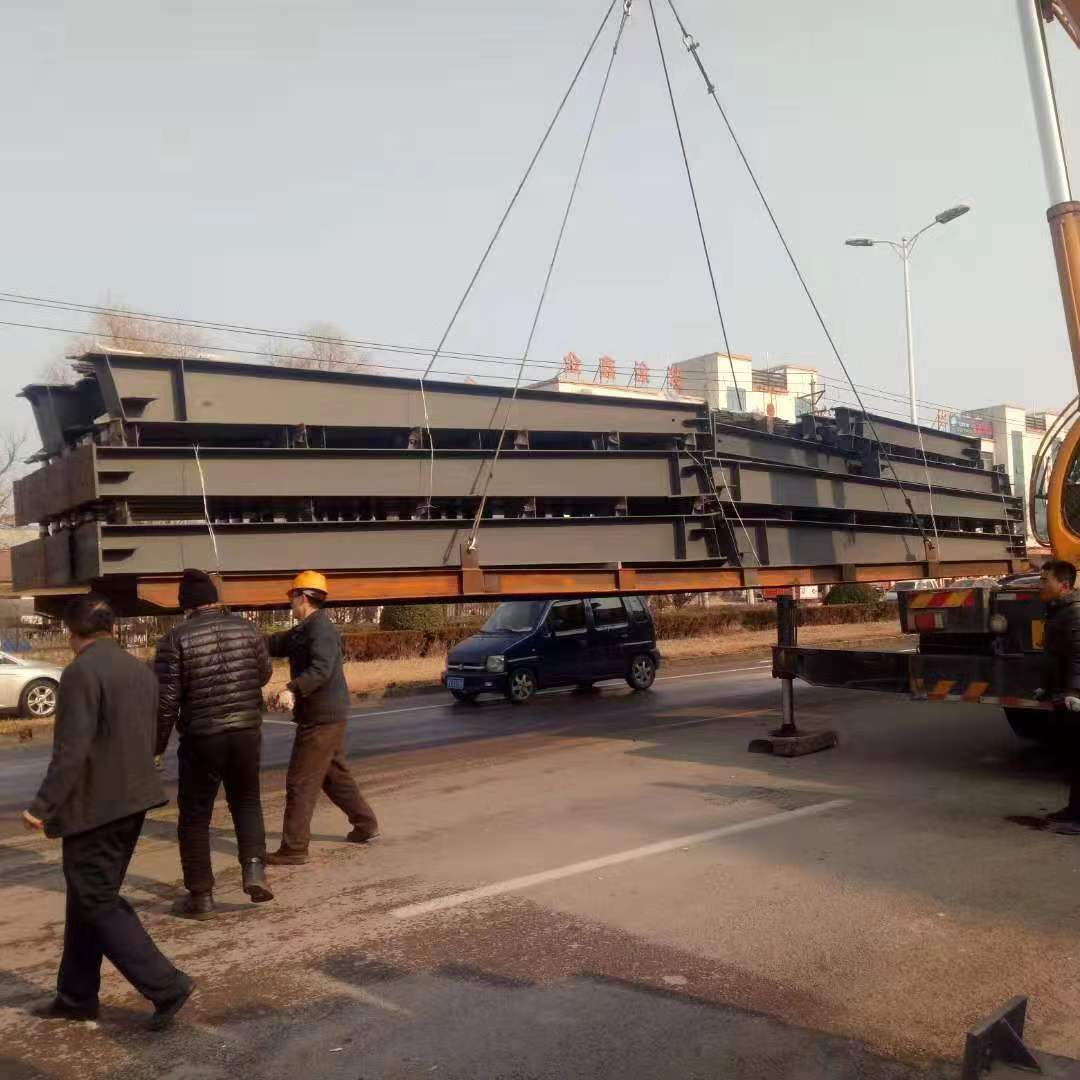
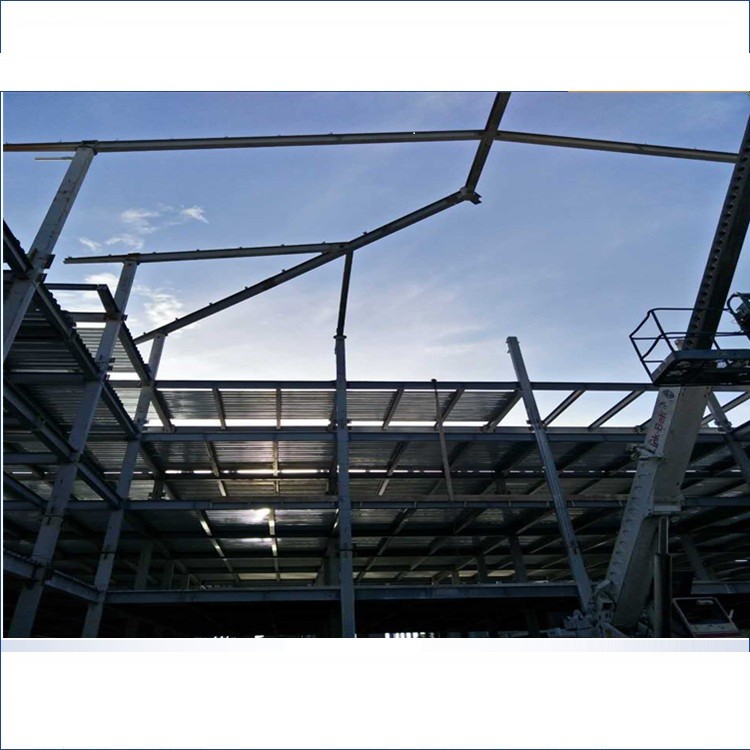
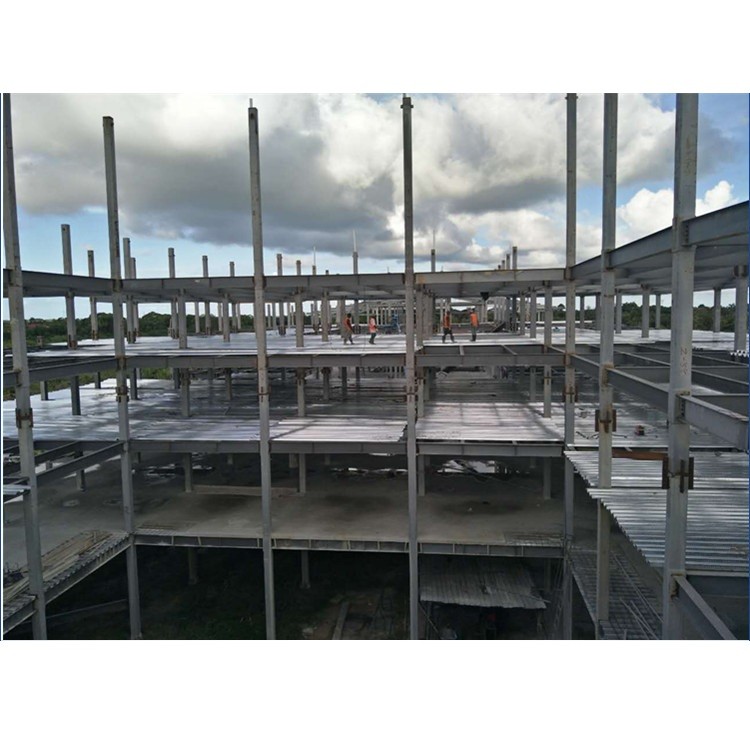
1、 Hoisting of steel structure column
1. Retest the foundation of steel structure workshop and steel structure warehouse, including the exposed length of anchor bolt, the displacement deviation of anchor bolt center line to datum line, anchor bolt spacing and foundation elevation. The unqualified ones can be hoisted after treatment.
2. In order to control the installation elevation of the column, the position of 500mm is marked on the visible section of the column in advance, so as to fine tune and correct the elevation during installation. The steel column shall be installed on the basis of qualified retest. Firstly, the column shall be bound with a single wire rope, and the position of lifting point shall be 1 / 3 of the column length from the column end. The column is hoisted by rotating method, and the steel column is hoisted to the installation position. The binding place shall be padded.
2、 Correction of steel structure column
1. Draw the center line on the visible surface of the column in advance, and then adjust the verticality of the column with theodolite in two mutually perpendicular directions.
2. The verticality of the column is controlled by measuring the distance between the inner side of the column and the control line on the building.
3. The adjustment of column elevation, axis and perpendicularity deviation is interrelated and takes into account, and the correction work can be completed only when all standards are met.
Section 3 installation technology of steel structure beam
The steel beam is unloaded to the vicinity of each column, transported to the floor by truck crane, and then installed by mast crane. Some main beams with heavy components can be hoisted with truck crane. The secondary beam can be installed by self-made tire crane (5T). Starting from the third zone, the main beam first, then the secondary beam, and then the purlin, the steel beam shall be hoisted by mast one by one according to the number. Only when the installation bolts at both ends of the beam are fastened (or the spot welding is firm), the hook can be loosened and other steel beams can be hoisted in turn. Welding shall be carried out after passing the inspection.
The binding and lifting point of steel beam is particularly important. If the steel beam is too long, the steel shoulder pole can be used. In this project, many steel beams are about 20m long at most. The triangular hanging plate is used to enlarge the distance between steel ropes to increase the angle between steel ropes, which meets the requirements of this hoisting. Steel beam binding diagram.
Section 4 on site welding process of steel structure
1、 Welding process of main components
Manual welding should adopt multi-layer, multi-channel and low current welding method.
1. Butt penetration weld (flat position manual arc welding)
It is suitable for butt weld of beam column flange plate and web, welding rod E4303. Welding process parameters:
Welding groove: B ≤ 12mm, single groove angle 60 degrees, blunt edge 2mm
b> 12mm double groove angle 60 degree, blunt edge 2mm, assembly clearance: 2-3mm
Welding current 140 ~ ~ 180A, welding voltage 24 V, welding speed 375 PX / min
2. T-weld (manual arc welding of ship shape)
It is suitable for beam column rib plate, connecting plate, column top plate, column bottom plate, double side fillet weld, welding rod E4303.
3. Welding process parameters:
Leg height: greater than the thickness of the thinner part of the weldment. Welding current 140 ~ ~ 160A, welding voltage 22V, welding speed 400px / min, manual arc welding can refer to the following table parameters:
Electrode diameter
Φ3.2
Φ4.0
Φ5.0
Welding current (a)
100~130
160~210
210~270
4. Weld appearance: check the weld appearance defects and weld leg size with naked eyes and measuring tools, which shall meet the requirements of construction drawings and construction specifications. The welding wave shall be uniform, and there shall be no defects such as cracks, lack of fusion, slag inclusion, overlap, undercut, burn through, crater and needle hole. The welding area shall be cleaned up and free of splash residue.
5. The full penetration weld is the key and key quality control point in the welding process. The quality inspectors should track and inspect this part and make corresponding quality inspection records.
Section 5 safety requirements for hoisting construction
1、 Civilized construction
1. Observe the management regulations of site safety, wear safety helmet when entering the site, and do not smoke.
2. The components are stacked and the electric welding machines are arranged in order. The spare oxygen and acetylene cylinders are put into special cages and placed separately.
3. Set up safety officer and fire prevention officer on site.
4. Keep the site clean.
5. All construction personnel on site obey the command and behave in a civilized manner.
2、 Safety technical measures
1. Transportation of components
① During loading, the components shall be padded with 10x10 timber square and sealed with 2T chain block.
② After loading, the overall height is less than 4m.
③ Driving speed ≤ 40 km / h, turning or uneven road ≤ 20 km / h.
④ The contact between the component and the wire rope shall be padded with rubber.
⑤ After loading, it should be placed in the middle of the car, and the front and rear parts should be sealed with 2T chains (three lanes should be sealed when transporting the middle part). During the transportation of all components, it is necessary to frequently check the sealing rope and chain fall of components, and deal with problems in time.
⑥ Because there are super long components, they should be transported at night. Safety disclosure should be carried out before transportation, and a special person in charge of transportation is required. The company is required to send full-time safety officers. Transport vehicles should be equipped with side lights. There should be vehicles driving in front and vehicles pressing behind. And we should negotiate with the transportation department about the specific time and route to ensure the smooth traffic.
2. Malaysia, Thailand, Indonesia, Philippines, Maldives and Southeast Asia purchased steel structure warehouse and steel structure workshop from China. The construction measures are as follows:
① Perpendicularity of the column: draw the center line on the two mutually perpendicular sections of the column in advance, and then calibrate the two theodolites on the two mutually perpendicular direction frames.
② Column center line to positioning axis: when retesting, pop up the center line of the foundation on the foundation, and draw the center line on the column. When installing the first section, make the center line of the column coincide with the center line of the foundation.
3. Finished product protection
① When transporting components, vehicles shall be selected according to the length and weight of steel components, and steel components shall be transported with three fulcrums (with logs).
② The storage site of steel members is flat and solid without ponding. When the steel members of the same type are stacked, the fulcrum of each layer of steel members is on the same vertical line.
3、 Others
1. Safety helmet must be worn when entering the construction site, anti-skid shoes and safety belt must be worn when working high above the ground. Personnel who are not suitable for working high above the ground are not allowed to work high above the ground.
2. Before the construction, the foreman shall lead the relevant personnel to inspect the rigging, and it can be used only after it is qualified.
3. It is forbidden to work when the wind is above level 4.
4. The hoisting operators shall strictly implement the "ten no hoisting" provisions in the "safety regulations", and the safety officer shall carry out safety education for the operators before hoisting.
5. In the process of hoisting, it is necessary to wait for the component to be in place before moving forward. When the sling of the component is untied, the safety belt should be tied firmly to prevent falling in the air.
6. The distance between the hoisting operation point and the high voltage line shall not be less than 2m. The distance from the low voltage line shall not be less than 1m, otherwise measures shall be taken before construction.
7. On the same vertical line, it is strictly forbidden to work up and down at the same time.
8. Working at height. All kinds of tools and accessories should be put into the tool bag, and it is strictly forbidden to throw or throw at random to prevent objects from hitting.
9. The component shall be in place smoothly to avoid vibration and swing. The sling can be loosened after the component is fastened.
10. Oxygen cylinders and acetylene cylinders for construction must be more than 10 m away from the open fire, and the distance between them must be more than 10 m, so as to avoid sun exposure and barbecue. Collision is prohibited when moving to prevent fire.
11. Qualified electrical equipment should be used and a special electrician should be responsible for it.